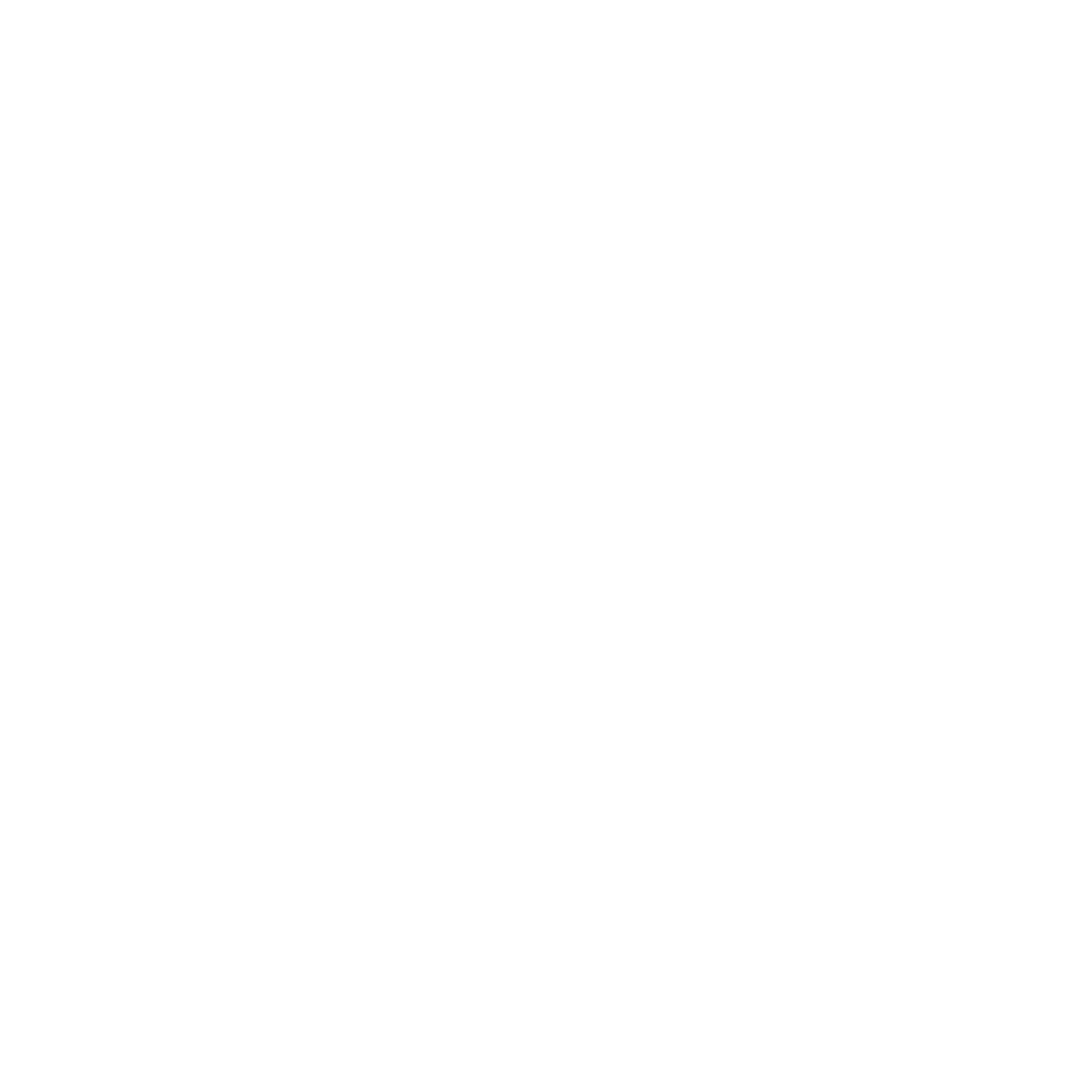
The tool magazine takes over parts automation.
High-tech components that are used for chip production can now be easily manufactured unmanned during the night shift. Photo: Harald Klieber.
The 5-axis department at Hittech Prontor recently started using a DMU 50 in three shifts because the raw and finished parts are clamped in the tool magazine with the Haubex System made by Lang.
In other words, it can be done without major automation and without major investment. “We bought the Haubex System from LANG Technik GmbH . This means that we are now able to manufacture our high-tech components, which are used for chip production, unmanned in the late and night shifts”, reports Ralf Tomka, Milling Team Leader at Hittech Prontor GmbH in Bad Wildbad. Located 30 kilometres south of Pforzheim, Prontor, founded in 1902, has been an important production site for ZEISS Medical Technology for 70 years, and has been an important machining authority for 5-axis machining in the Dutch Hittech Group since 2014.
A focus on the most automated raw part handling where possible.
The main markets, according to Production Manager Marco Doose, are primarily the medical technology and semiconductor lithography sectors. “Automotive was never really our focus. At the moment, we are investing heavily in new machining equipment, which of course needs to be more automated than ever for our three-shift production.” When selecting machines, the focus would be on off-the-shelf machining or on handling raw parts as automatically as possible. As Marco Doose explains, this would also maximise flexibility for the component assignment to the machines in the future.
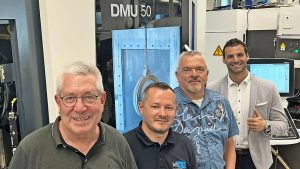
The experts Marco Doose (from the left), Ralf Tomka, Waldemar Stapauk and Fabio Rinaldo. Photo: Harald Klieber.
“The simplest automation solution in the world.”
Prontor has had positive experiences with the automation experts from Lang Technik, in particular when it comes to handling raw parts. “We have been working with Lang since 2012. It all started with an Eco-Tower, which still contains up to 60 Makro-Grip vices clamping in raw parts for milling. However, we have recently been very impressed by the Haubex System, which our programmers discovered on the Lang website and found to be the ideal solution for improving the utilisation of one of our DMU 50 machining centres”, explains Ralf Tomka.
According to Application Consultant Fabio Rinaldo , Lang Technik currently only offers the automatic clamping device change from the tool magazine in one size, but it has a lot to offer: “The Haubex System really is the simplest automation solution in the world. This is because Haubex inserts the pre-clamped blank together with the 5-axis clamp in the clamping device housing directly from the tool magazine into the machine spindle like a tool.” The spindle then places the clamp together with the blank in the zero-point clamping system on the machining table, unlocks the housing with a 90° rotation, which is replaced with the first cutting tool for part machining and then disappears into the tool magazine.
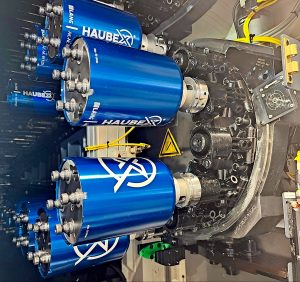
More components will soon be clamped in the tool magazine using the Haubex System and then manufactured on the DMU 50. Photo: Harald Klieber.
Productivity more than doubled.
Prontor has achieved considerable savings with the Haubex System, which clamps workpieces in dimensions up to 80x75x70 mm. “Without Haubex, we were previously producing around five parts in one shift. With Haubex, we now easily produce ten parts. Not only have we more than doubled productivity, but we have also utilised the previously unused spindle capacities of the late and night shifts on this DMU 50 with a very small investment.” The components can now be fully milled and deburred on five sides, machine operator Waldemar Stapauk reports. The next day, the components only have to be finished on the sixth side and the ten Haubex clamping device housings fitted with new workpieces.
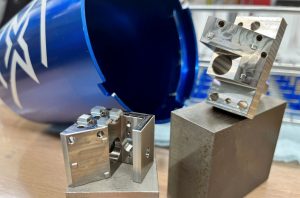
The cubic part (left) is precision-milled, drilled and reamed with 20 tools in around 52 minutes. Another 20 tools are used to shape the narrow part (right) in around 90 minutes. Photo: Harald Klieber.
“Haubex really is a fantastic system for machinists who don’t yet have automation or who want to significantly improve their milling times on a budget. We have achieved the latter perfectly thanks to the high capacity utilisation of the DMU 50 in the late and night shifts”, Ralf Tomka summarises. Although Prontor had not made it easy for itself with the machining of the parts from the tough Invar 36 tool steel: The cubic part is milled, drilled and reamed precisely with 20 tools in around 52 minutes – including two fits with a diameter of 0.8 mm, which are machined with a tolerance of +0.025/+0.040. Another 20 tools shape the narrow part in around 90 minutes – including two opposing functional surfaces, which are manufactured with a shape and position tolerance of 0.02 mm.
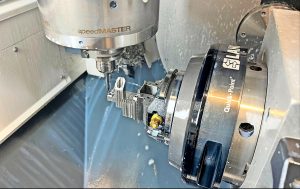
For the narrow part, two opposing functional surfaces must be manufactured with a form and position tolerance of 0.02 mm. Photo: Harald Klieber.
Sustainability and a small footprint.
In addition, Marco Doose emphasises that very little additional space is required for the Haubex System, neither robots nor peripheral devices need to be purchased and placed on the machine, only a small part of the tool magazine needs to be freed up. “Sustainability and low space requirements are of course beneficial side effects for us because the topic of the CO2 footprint has also reached us in Bad Wildbad, and we hardly have any free space in our 5-axis machining department. That’s why we are paying ever more attention to the important automation features of tool measurement and tool breakage detection when purchasing machines in the future, as well as a large tool magazine with preferably well over 100 tool slots, so that we can of course also accommodate a sufficient number of sister tools.”
Thanks to Harald Klieber for writing the original article and making the photos for NCFertigung .